BITUTHENE® 5000
Composite membrane incorporating high performance moisture and water-resistant rubberised asphalt with tough, puncture and heat-resistant polypropylene reinforcing mesh. Specially developed for use under a hot applied asphalt concrete wearing course.
Product Description
BITUTHENE® 5000, also known as Heavy Duty Bituthene, is a waterproofing material incorporating high strength, heat-resistant mesh embedded in a layer of self-adhesive rubberised asphalt. It is supplied in rolls interwound with special release paper which protects the adhesive surface until ready for use and allows easy handling during installation.
Features
-
Cold applied — no heating or hot bitumen bedding adhesive required, self-adhesive overlaps provide continuity.
-
Flexible — easily applied, conforms to changes in profile, accommodates shrinkage cracks up to 0.6mm.
-
Robust — accepts road-laying machinery.
-
Preformed — guaranteed thickness, not subject to site variation.
-
Mesh reinforced — provides dimensional stability and resistance to damage.
-
Rubber/bitumen — self-adhesive, elastic compound provides bonding and transmission of braking forces to substrate, allows healing of small punctures.
Application
Bituthene 5000 is supplied in rolls 1.00m wide, 20.0m long and in min. membrane thickness of 1.6mm and 2.0mm. The rubberised asphalt is covered with release paper that is removed during installation. The membrane is self-adhesive and cold applied. No special adhesive or equipment is necessary to form laps. Bituthene 5000 is an excellent waterproofing membrane for plazas, bridges, vehicular traffic structures, or parking decks to be overlaid with an asphalt concrete wearing course. It is adaptable for either new construction or repair applications.
Bituthene S5000 strips are recommended for the restoration of concrete pavements with asphalt concrete overlays to prevent premature deterioration of asphalt paving over the transverse and longitudinal joints caused by reflection cracking and sub-base erosion. Bituthene 5000 membrane will remain flexible to perform over the extreme range of service temperatures expected on plazas,bridges, and parking decks. Its toughness and flexibility allow it to cycle over small cracks, even during critical winter months.
The membrane is highly resistant to water and deicing salt solutions. Electrical resistance measurements on structures have been exceptionally high to indicate the effectiveness of Bituthene 5000 in preventing water migration into decks.
Installation
Surface Preparation
Smooth, monolithic concrete surfaces are required for proper membrane adhesion. Surfaces must be free of voids, spalled areas, loose aggregates, and sharp protrusions, with no coarse aggregate visible. Broom finishes must not be used. Concrete must be cured and dry before applications of Bituthene 5000.
Clean surface (broom, vacuum cleaner or compressed air) to remove dust, loose stones, and debris.
Performance
Property | Typical Test Values | Test Method |
---|---|---|
Thickness* | 1.6 mm or 2 mm | |
Tensile Strength - Mesh | 10N/mm2 | ASTM D882 |
Elongation - Ultimate Failure of Rubberised Asphalt |
>100% | ASTM D412 |
Pliability at Low Temperature (-32°C) |
No damage | ASTM D1970 |
Puncture Resistance - Mesh | >900N | ASTM E-154 |
Priming
Apply Primer, Bituthene Primer, to all concrete or masonry surfaces with a lambswool roller (6 ~ 8m2 per litre). Allow primer to dry one hour or until tack free. Prime only the area which will be covered with membrane in a working day. Areas not covered with membrane in 24 hours must be reprimed.
Temperature
Apply Bituthene 5000 waterproofing membrane only in fair weather when air and surface temperature are above +5°C.
Slab Drainage and Joints
Provide proper pitch to drains and gutters. Bituthene 5000 should be laid from the low point to the high point with the membrane overlapped min. 50mm in shingle fashion. Weep holes or drainage openings should be provided at the structural deck level to drain water which penetrates the asphalt concrete. A 320 mm reinforcing strip of Bituthene 5000 must be applied over nonworking joints or cracks not exceeding 3mm in width before applying the full coverage of membrane. Terminate Bituthene 5000 at expansion joints and seal terminations with Bituthene Mastic at the termination to ensure a tight seal. Steel finger joints or other expansion joints assemblies should be placed to the level of the asphalt concrete overlay.
Kerb and Termination Edges
Kerb flashing strips should be applied to a joint just below the height of the asphalt concrete overlay and a minimum of 150 mm on the deck. Then apply the first full sheet as close as possible to the kerb. A fillet should be provided at the kerb and parapets to avoid a sharp break at these points. The fillet material (latex modified cement mortar) should be well adhered to the deck and kerb or parapet. Performed cant strips are not recommended.
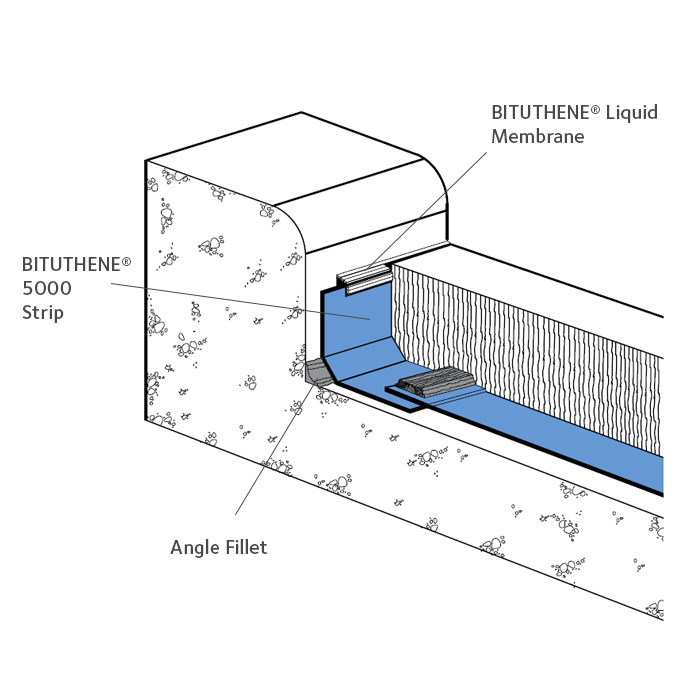
Supply
Bituthene 5000
1.6mm thick - 1.0m wide x 20.0m long/roll 2.0mm thick - 1.0m wide x 16.0m long/roll
Weight: Gross weight 40kg
Bituthene Primer
18L / pail (6 ~ 8 sq m / L)
Bituthene Mastic
850cc cartridges / 3L cans
Compatibility
Bituthene 5000 is incompatible with certain fresh tars, pitches, liquid waterproofing, and sealants which contains tars or polysulfide polymer. Avoid direct contact of the adhesive layer of Bituthene 5000 or Bituthene Mastic with such systems.
Paving
The asphalt concrete overlay should be placed as soon as possible after application of Bituthene 5000, or Bituthene S5000. A minimum of 50 mm compacted overlay is recommended. The preferred asphalt concrete temperature in the paving machine hopper is 140°C to 160°C. Preformed protection courses such as roofing felts or asphaltic hardboard are not recommended. Paving must not be started following rain until the membrane surface is dry. Only asphalt concrete delivery equipment should be permitted on the membrane prior to placement of the asphalt concrete.
Flat tracked or pneumatic tire equipment may be used. In the event of skidding of the pneumatic tire machine during warm weather, broadcast a very small amount of fine sand or cement in the tire paths. Excess use of cement or sand could prevent adhesion of the asphalt concrete. Pavers should avoid stopping with a full hopper or build up of material in the auger. If a stop is necessary, use extreme care in restarting. Paver screeds should be preheated, but burners should not be on during paving.
Precautions
Care should be taken to minimise the possibility of pavement shoving on heavy traffic structures with more than a 4% grade. Bituthene S5000 strips over joints in T beam structures will not provide complete waterproofing. For such structures, 320mm strips, followed by membrane coverage over the entire surface are required to provide a complete waterproofing system.
Health and Safety
Refer to relevant Material Health and Safety data sheets.
Quality Assurance
GCP Applied Technologies is certified to ISO 9002 by TUV SUD PSB Pte Ltd..
Specification
All areas so designated shall be waterproofed with a minimum 1.6mm or 2.0mm thick self-adhering membrane of rubberised asphalt integrally bonded to polypropylene mesh (Bituthene 5000 manufactured by GCP Applied Technologies). Bituthene 5000 set pre-formed self-adhesive membrane shall be laid onto smooth concrete primed with Primer B1 and with minimum overlaps of 50 mm. Bituthene 5000 must be laid strictly in accordance with Manufacturers instructions and supplied by GCP Applied Technologies. For further information, contact your local GCP representative.
Technical Services
For assistance with working drawings for projects and additional technical advice, please contact GCP Applied Technologies.
gcpat.id | For technical information: asia.enq@gcpat.com
We hope the information here will be helpful. It is based on data and knowledge considered to be true and accurate, and is offered for consideration, investigation and verification by the user, but we do not warrant the results to be obtained. Please read all statements, recommendations, and suggestions in conjunction with our conditions of sale, which apply to all goods supplied by us. No statement, recommendation, or suggestion is intended for any use that would infringe any patent, copyright, or other third party right.
Bituthene is a trademark, which may be registered in the United States and/or other countries, of GCP Applied Technologies, Inc. This trademark list has been compiled using available published information as of the publication date and may not accurately reflect current trademark ownership or status.
© Copyright 2024 GCP Applied Technologies, Inc. All rights reserved.
GCP Applied Technologies Inc., 2325 Lakeview Parkway, Alpharetta, GA 30009, USA
PT GCP Applied Technologies Indonesia, Cikarang Industrial Estate Kav C-32, Cikarang, Bekasi 17530
This document is only current as of the last updated date stated below and is valid only for use in Indonesia. It is important that you always refer to the currently available information at the URL below to provide the most current product information at the time of use. Additional literature such as Contractor Manuals, Technical Bulletins, Detail Drawings and detailing recommendations and other relevant documents are also available on www.gcpat.id. Information found on other websites must not be relied upon, as they may not be up-to-date or applicable to the conditions in your location and we do not accept any responsibility for their content. If there are any conflicts or if you need more information, please contact GCP Customer Service.
Last Updated: 2025-05-19
https://gcpat.id/en-gb/solutions/products/bituthene-post-applied-waterproofing/bituthene-5000