Best practices for waterproofing buried roofs
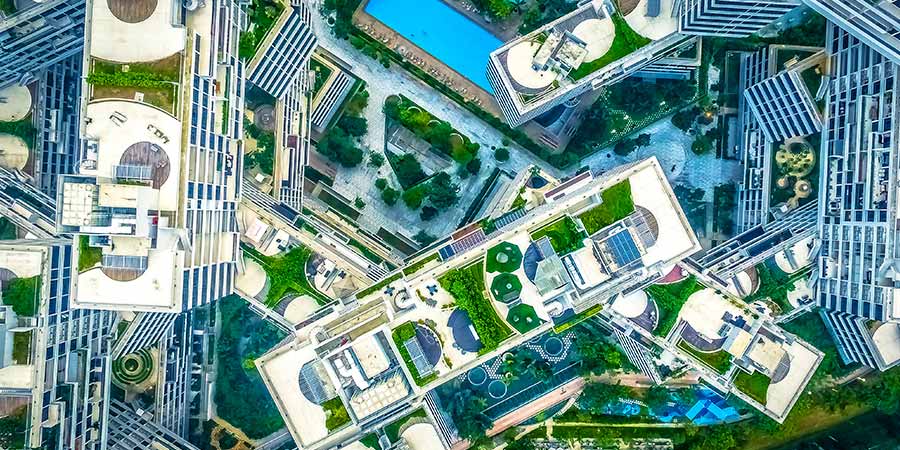
What are buried roofs?
Typically part of an under-garden structure or landscaped area, a buried roof is either part of a basement that extends beyond the line of the main elevations, or an elevated deck accessible by people or traffic.
Challenges of buried roof waterproofing
During construction, buried roofs often become part of the working platform for the crew, and provide access to the building itself. The timing of waterproofing the buried roof becomes critical. It needs to be done at a point when it doesn’t restrict access to the building, but it also needs to be done early enough to keep the building weather tight.
In addition, the waterproofing system for buried roofs needs to be particularly durable. Since the material will ultimately lie underneath landscaping or other finishes, it becomes very disruptive to have to make repairs if leaks occur. You would have to remove the landscaping or other layer to identify where the leak is and then repair it. Because of this, waterproofing materials need to last for the life of the building itself.
Common pitfalls in waterproofing buried roofs
Waterproofing buried roofs can be challenging due to the number of complexities and details. If it’s a landscaped roof, for example, there are many penetrations for irrigation and drainage, and these penetrations are where there is the highest risk of a leak. Using liquid-applied waterproofing is an excellent choice for this type of application since it’s easier and faster to seal reliably around penetrations and corners with a liquid than with a sheet-applied waterproofing system.
Learn more about SILCOR® liquid waterproofing
Torch-applied sheet waterproofing can be used, but requires a high skill to deal with sheet overlaps properly, and to handle the hot works operation that is required for adhesion. When hot works are required, if the material is applied too hot it will burn and crack and if it’s too cold, it won’t adhere properly. Hot works are becoming less practical, due to the increasing safety concerns of working with an open flame. In the UK, for example, fire marshals must be on-site during hot works operations.
Tips for gaining long-lasting waterproofing protection
- Prevent water migration. Choose a waterproofing system, such as SILCOR®, that is fully bonded to the substrate. This way, if a leak occurs in the membrane, the water is trapped in one small area and can’t get underneath the membrane and into the building. With this approach, leaks are also much easier to repair because you can quickly pinpoint where they came from.
In addition, while some high performance, fully bonded liquid applied waterproofing systems can be applied to flat decks it’s good practice and generally recommended to slope structural decks.
- Ensure continuity. Choose a waterproofing system that’s compatible with the one used below ground. This will prevent gaps in coverage and disagreements over who is responsible. .
- Involve the waterproofing specialist early in the design phase. This way, the waterproofing system can be accurately designed as part of the structural buildup. As a specialist, the system manufacturer can provide suggestions for simplifying and optimising the waterproofing system.
- Choose a versatile waterproofing system. A buried roof might have a combination of hard and soft landscaping or other elements such as an access road or a parking garage, so you’ll need a system that is continuous and isn’t affected by different finishes.
- Look beyond the warranty. Ultimately, it’s the performance of the waterproofing membrane that’s most important. The best warranty in the world won’t protect against leaks, which can be quite disruptive to fix.
Tags
- Architects
- Building Envelope Solutions
- Consultant
- Contractor
- Developer
- Distributor
- Engineer
- Owner
- Silcor®
- Subcontractor
- Waterproofing